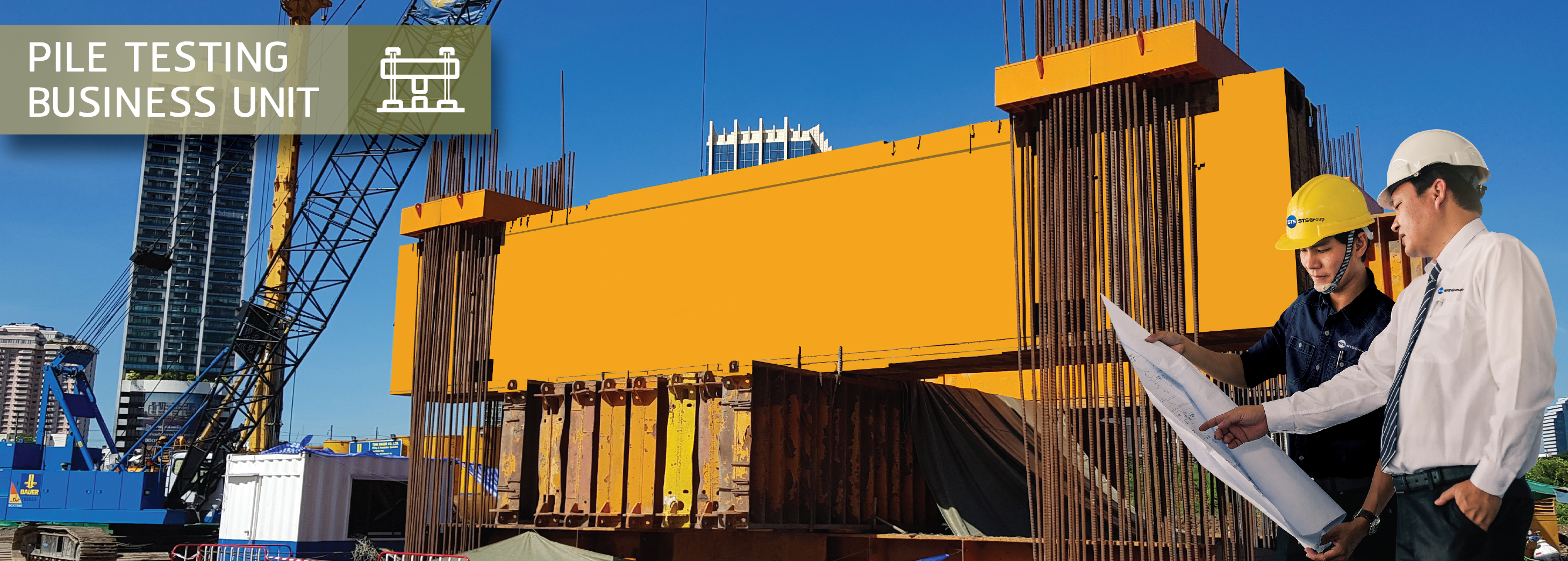
Pile Testing Business Unit
Pile testing is one of our businesses in STS Corporation Company Limited providing pile testing services, especially on testing work to assess the integrity and load capacity of piles.
By adhering to the great quality / international standard and accuracy, the company has gained trust from our existing customers on a small to large business scale both in government agencies and private sector projects. The service work of the pile testing unit consists of.
Pile Integrity Test
Pile Integrity test is the test to assess the integrity of the pile foundation In order to know the condition of the integrity of the pile structure. As the pile found that the condition is not perfect than the criteria used for acceptance, it may affect the ability of its capacity to withstand the bearing capacity as well. The pile integrity test method investigated by using stress wave such as the Low Strain Integrity Test (Seismic Test), Side Echo Test, and Single Shock End Test and Cross Hole Sonic Logging Test is the method which using Ultra Sonic Pulse Test in Inspection.
Low strain integrity test is one of the methods for assessing the condition of piles or shafts. It is cost-effective and not very time-consuming. This method is covered under ASTM D5882 Standard Test Method for Low Strain Integrity Testing of Piles.
The test is based on wave propagation theory. The name "low strain integrity test" stems from the fact that when a light impact is applied to a pile it produces a low strain. The impact produces a compression wave that travels down the pile at a constant wave speed. Changes in the cross-sectional area - such as a reduction in diameter - or material - such as a void in concrete - produce wave reflections.
This procedure is performed with a handheld hammer to generate an impact, an accelerometer or geophone placed on top of the pile to be tested to measure the response to the hammer impact, and a data acquisition and interpretation electronic instrument.
Moreover, This Scope of work in low Strain integrity test has been certified according to ISO9001:2015 standard which is the first and only testing company in Thailand that is certified in this section.
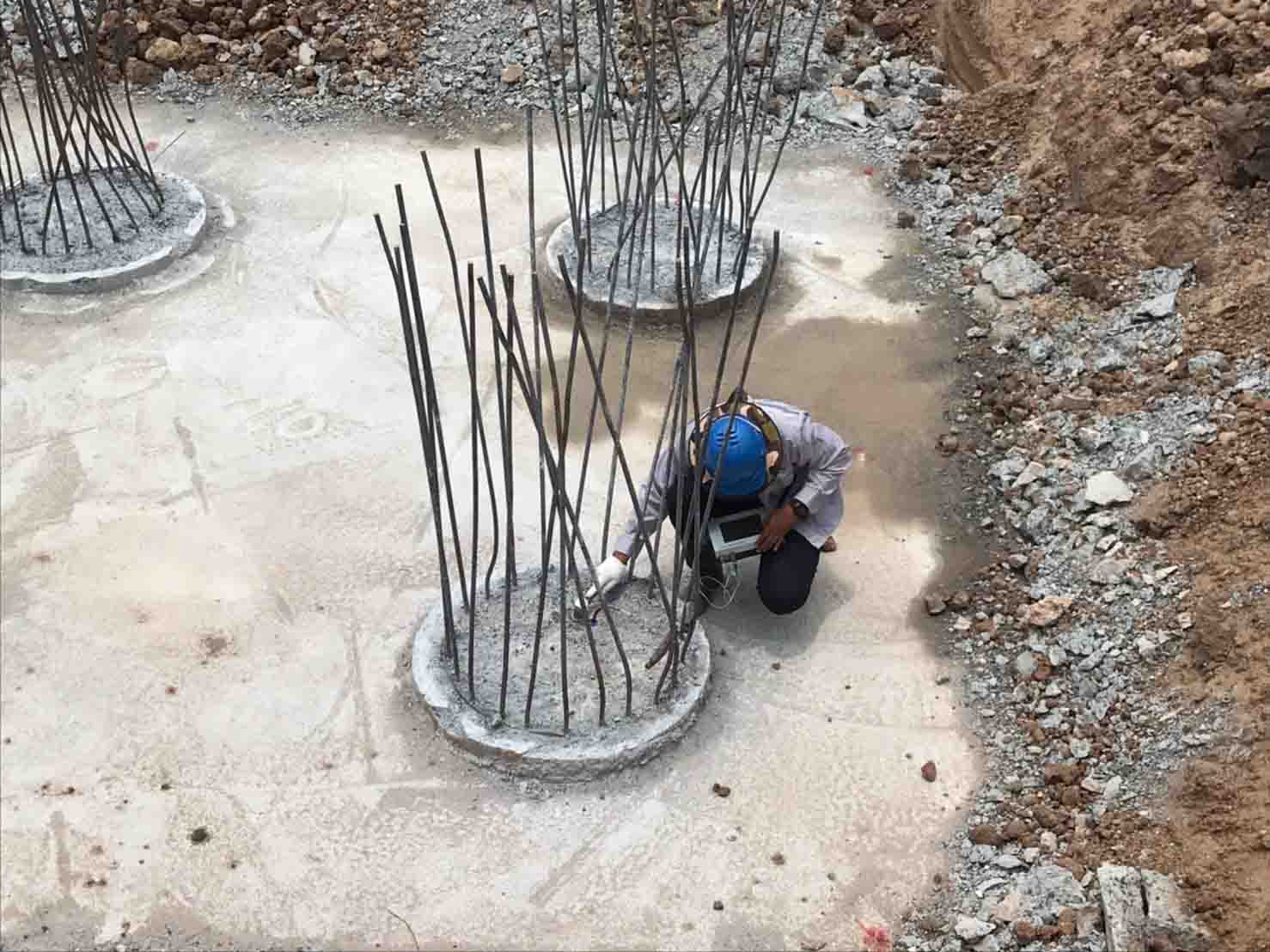
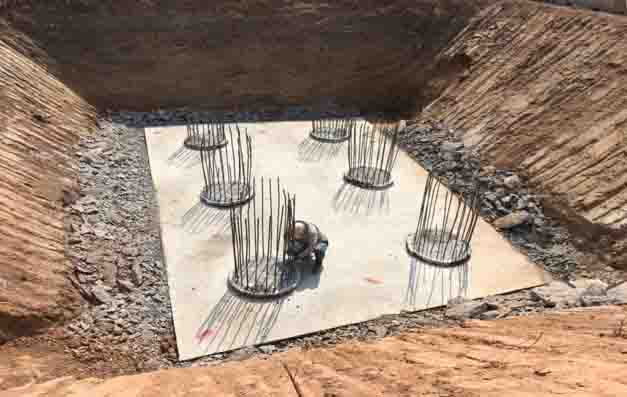
Side Echo Test
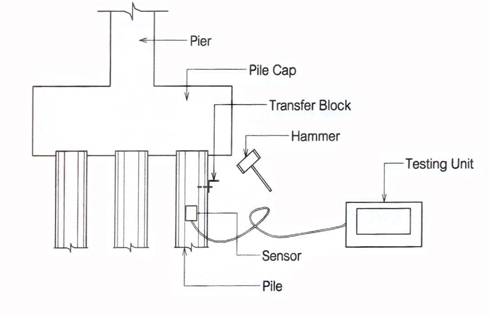
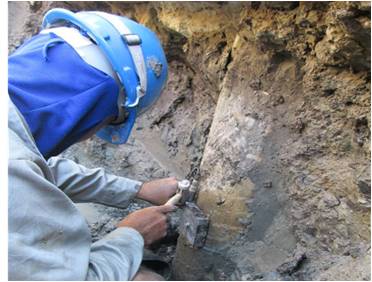
Single Shock End Test
1. Impact quality and concrete quality near the pile top
2. Pile defect along the investigated length
3. Approximated pile length (if possible)
4. Characteristic mobility (M) and Pile head dynamic Stiffness (E’)
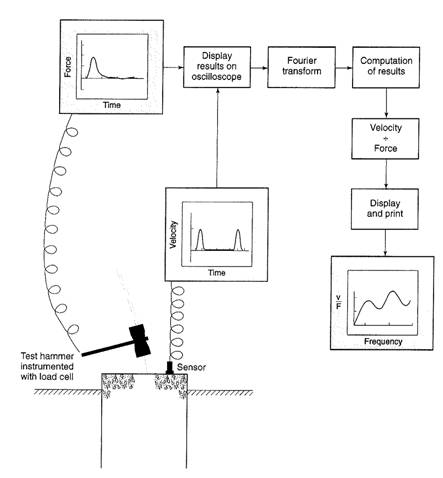
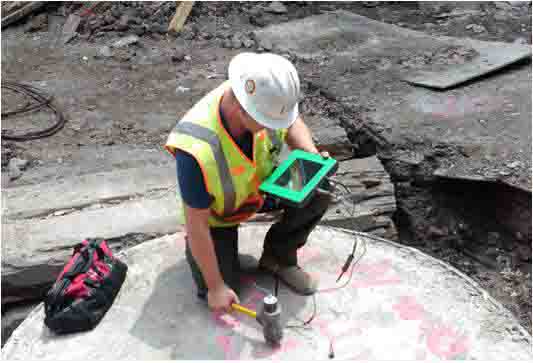
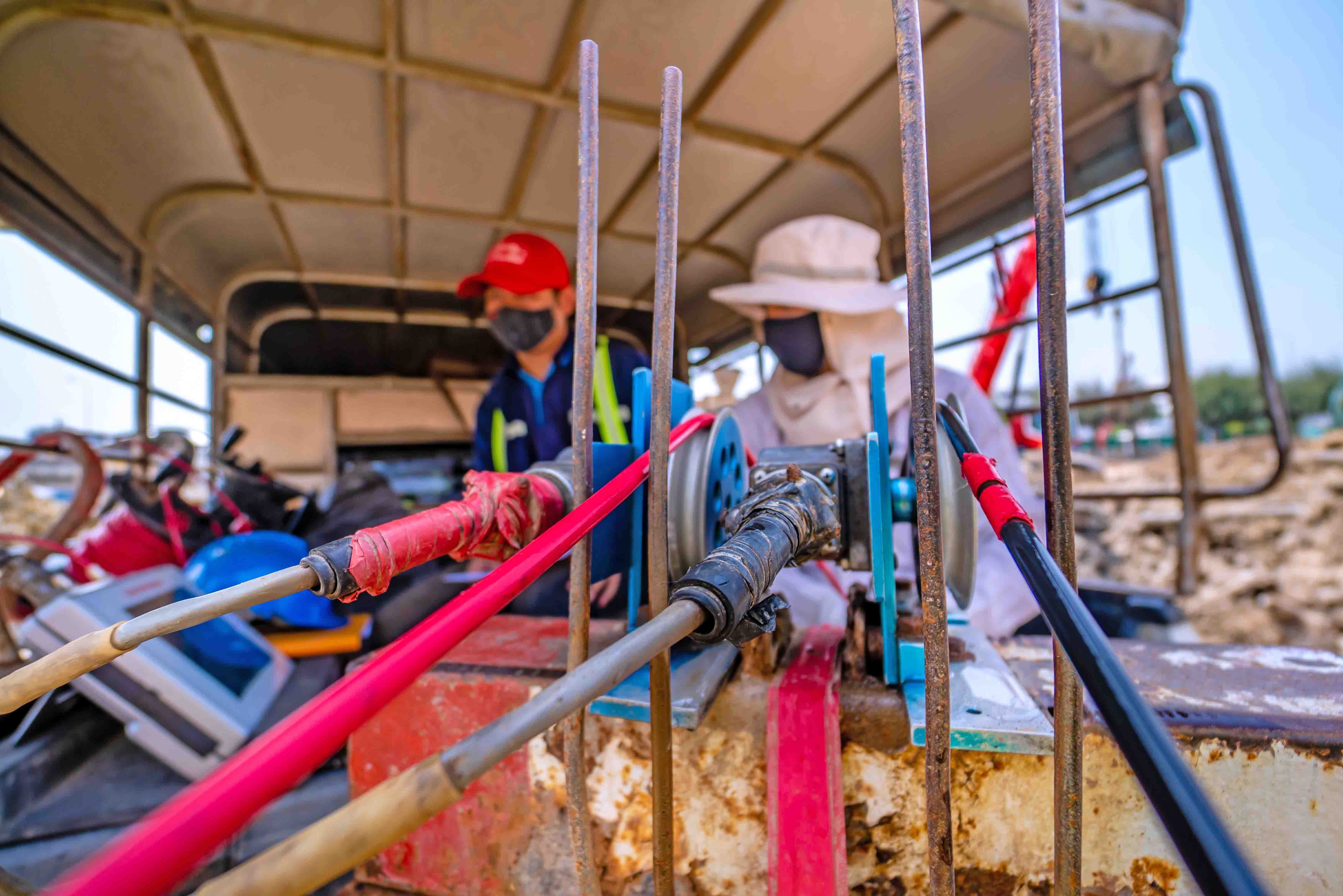
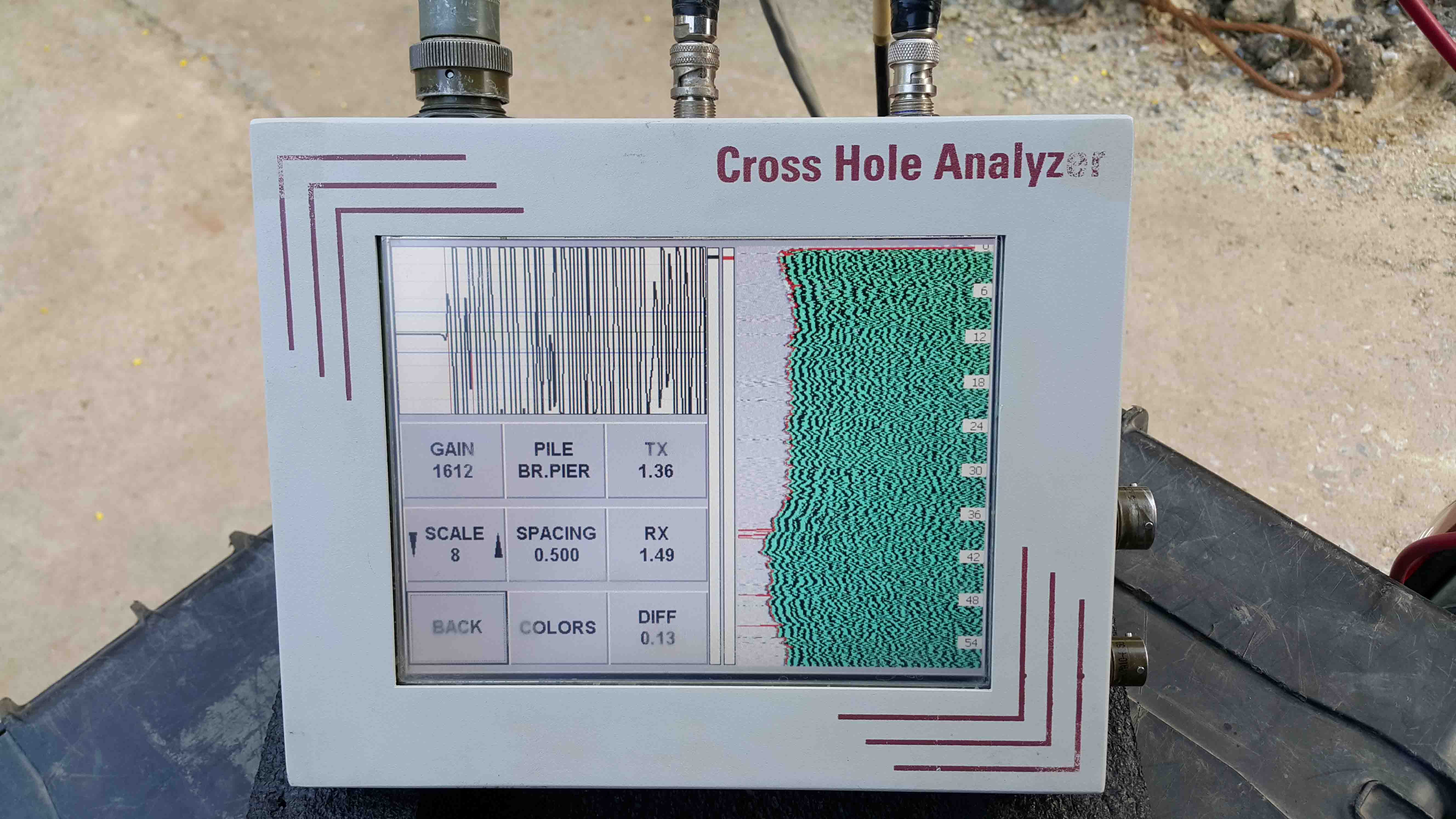
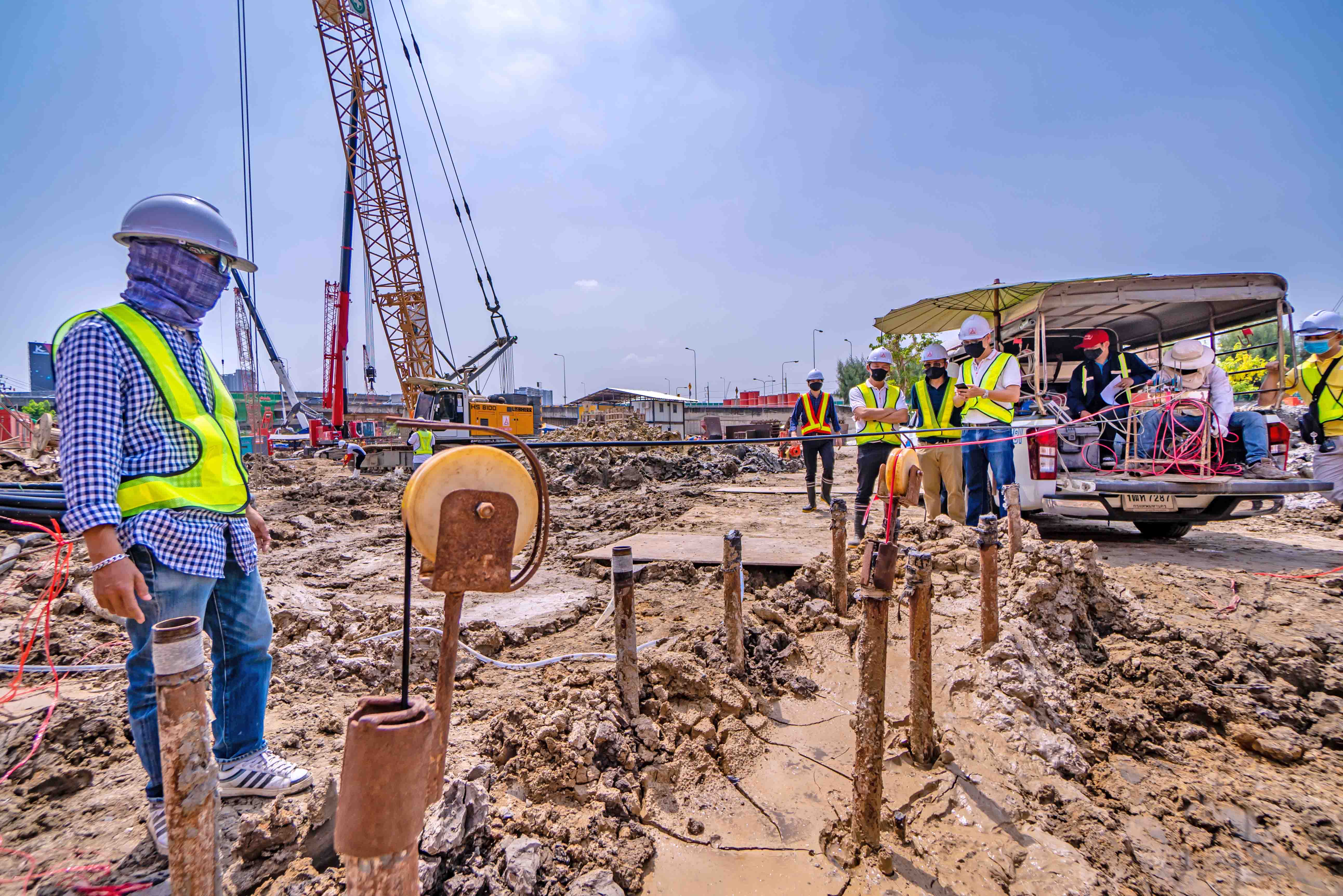
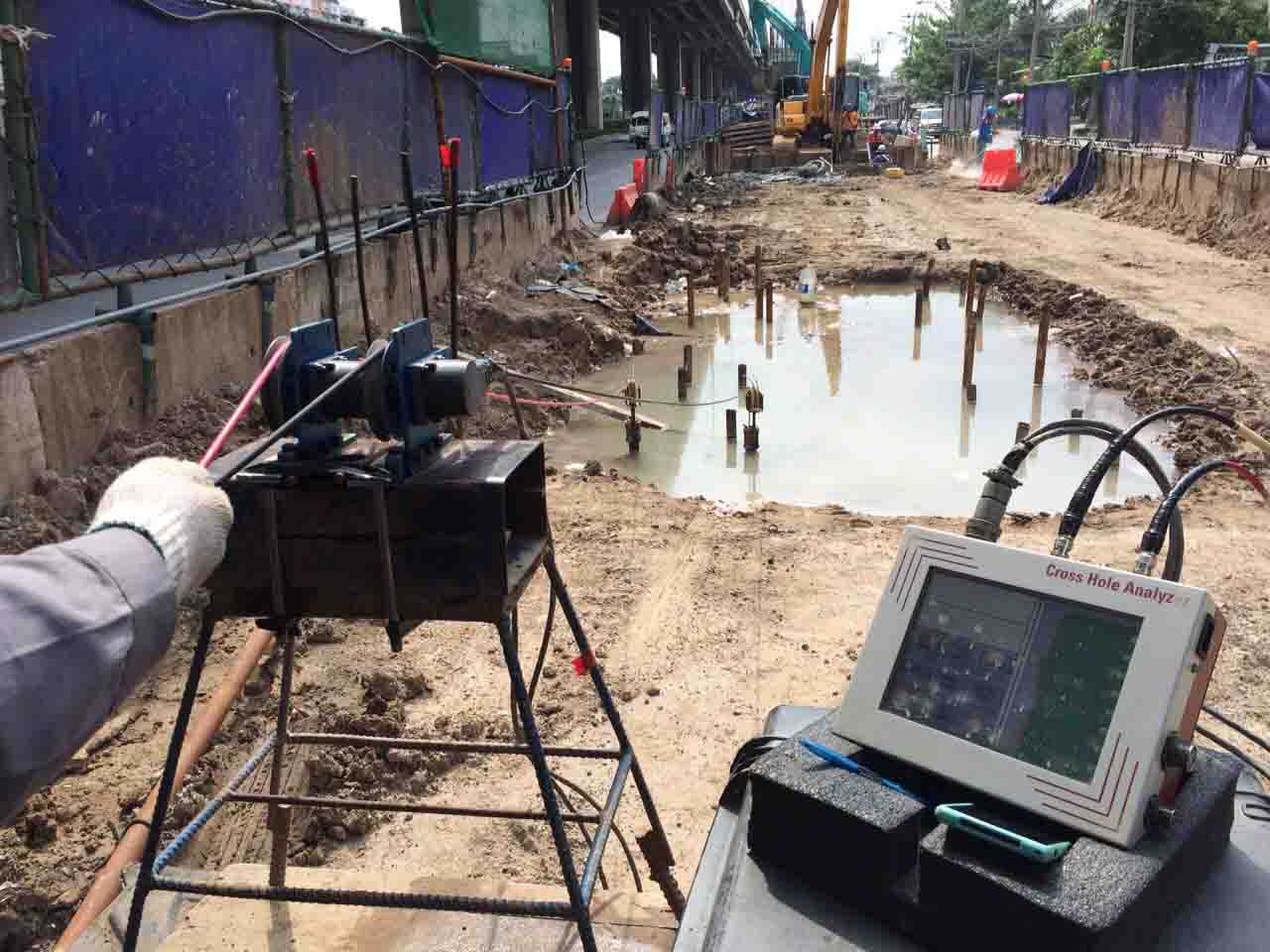
Pile Capacity Test
Static Pile Load Test
Full-scale static loading, conformed by ASTM D1143, is a widely accepted test method for the authoritative assessment of deep foundations. Testing is typically performed once and the result is considered the definitive answer regarding the pile’s load-bearing capacity.
The static pile load test is the most common method of testing the capacity of a pile and it is also considered to be the best measure of foundation suitability to resist anticipated design loads. The static load test involves the direct measurement of pile head displacement in the response to a physically applied test load. This test provides very reliable data for pile capacity.
This method is applicable to all kinds of pile types, over land or over water, and may be carried out on either production piles or test piles. Test piles are specifically constructed for the purpose of carrying out load tests and therefore, are commonly loaded to failure. Testing of production piles, however, is limited to prove that a pile will perform satisfactorily at the serviceability or design load, plus an overload to demonstrate that the pile has some reserve capacity.
Furthermore installed and measured instrumentation into the test pile such as strain gauge, fiber optic, and extensometer can be available to determine the soil parameters in order to verify and optimize the design of the foundation for a structure.
High Strain Dynamic Pile Load Test
High strain dynamic testing is a method of testing deep foundation to obtain information about their capacity and integrity, and in some cases, to monitor their installation. It is codified by ASTM D4945 Standard Test Method for High-Strain Dynamic Testing of Piles.
High strain dynamic testing is called dynamic pile monitoring when it is applied during pile driving and dynamic load testing when it is applied following pile installation, regardless of the installation method.
High strain dynamic testing consists of estimating soil resistance and its distribution from force and velocity measurements obtained near the top of a foundation impacted by a hammer or drop weight. The impact produces a compressive wave that travels down the shaft of the foundation.
A pair of strain transducers obtains the signals necessary to compute force, while measurements from a pair of accelerometers are integrated to yield velocity. These sensors are connected to an instrument (such as a pile driving analyzer), that records, processes, and displays data and results.
Bi-directional static loading test adopting load cells is widely used around the world at present, with an increase in diameter and length of deep foundations. The BDSLT method of pile load test utilizes hydraulically operated Cells embedded inside the concrete of the pile. The embedded load cell is specially designed using built-in hydraulic jacks. The pressure is applied to the load cell by a hydraulic pump on the ground through the flexible hose embedded into the pile. The pressure in the load cell is measured by a pressure transducer and the displacements are measured by displacement transducers which are connected to the load cell by a telltale rod embedded into the pile. When loaded the load cell expands, pushing the upper shaft upwards and the lower shaft downwards, which would mobilize the side resistance and base resistance of the upper and lower lengths of the pile.
According to the relationship between the movements, the bearing capacities of both the upper and lower portions of the pile can be determined. Adding up the modified side resistance of the upward pile shaft and the base resistance of the downward pile shaft makes up the total ultimate bearing capacity of the pile.
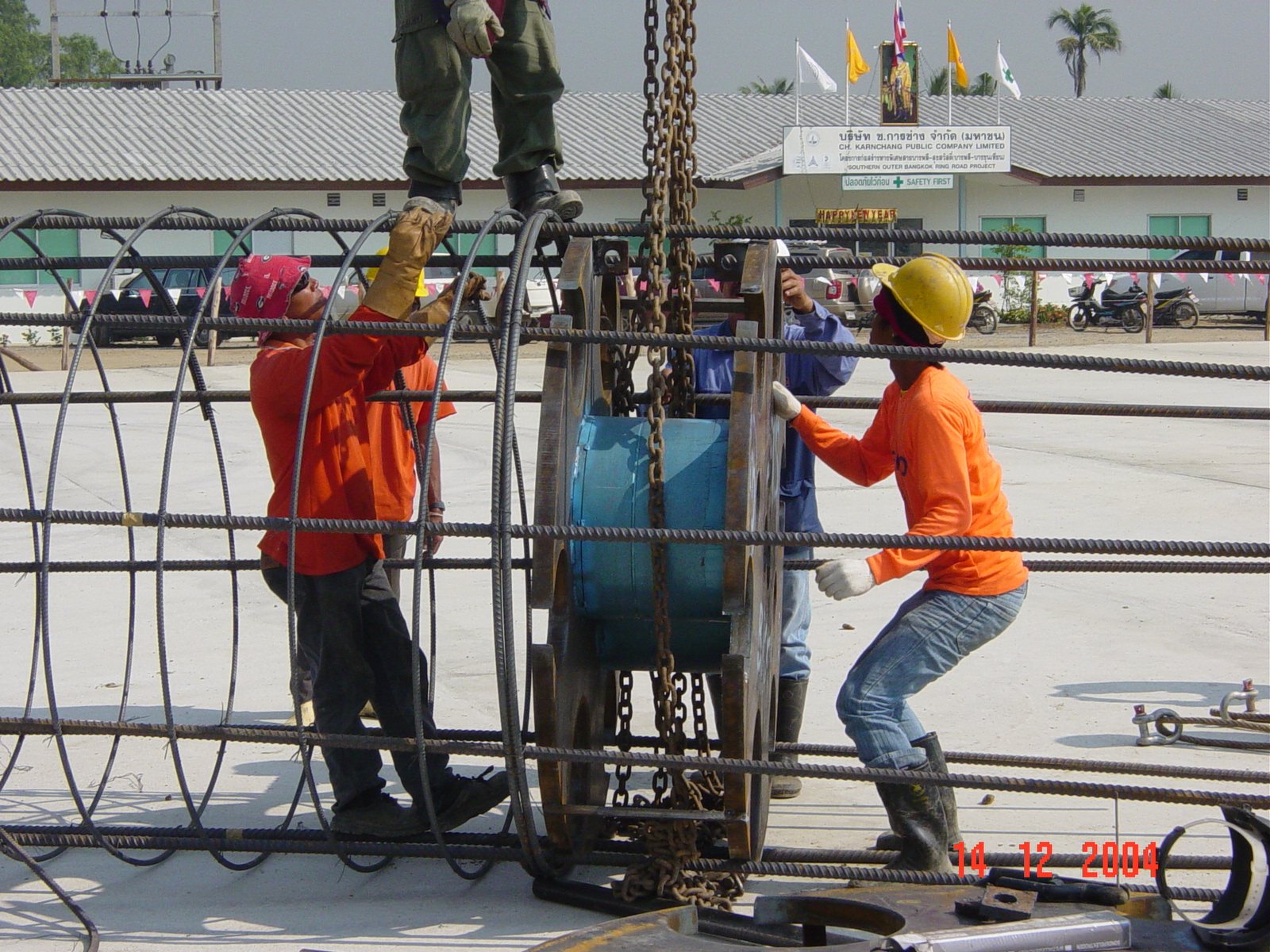
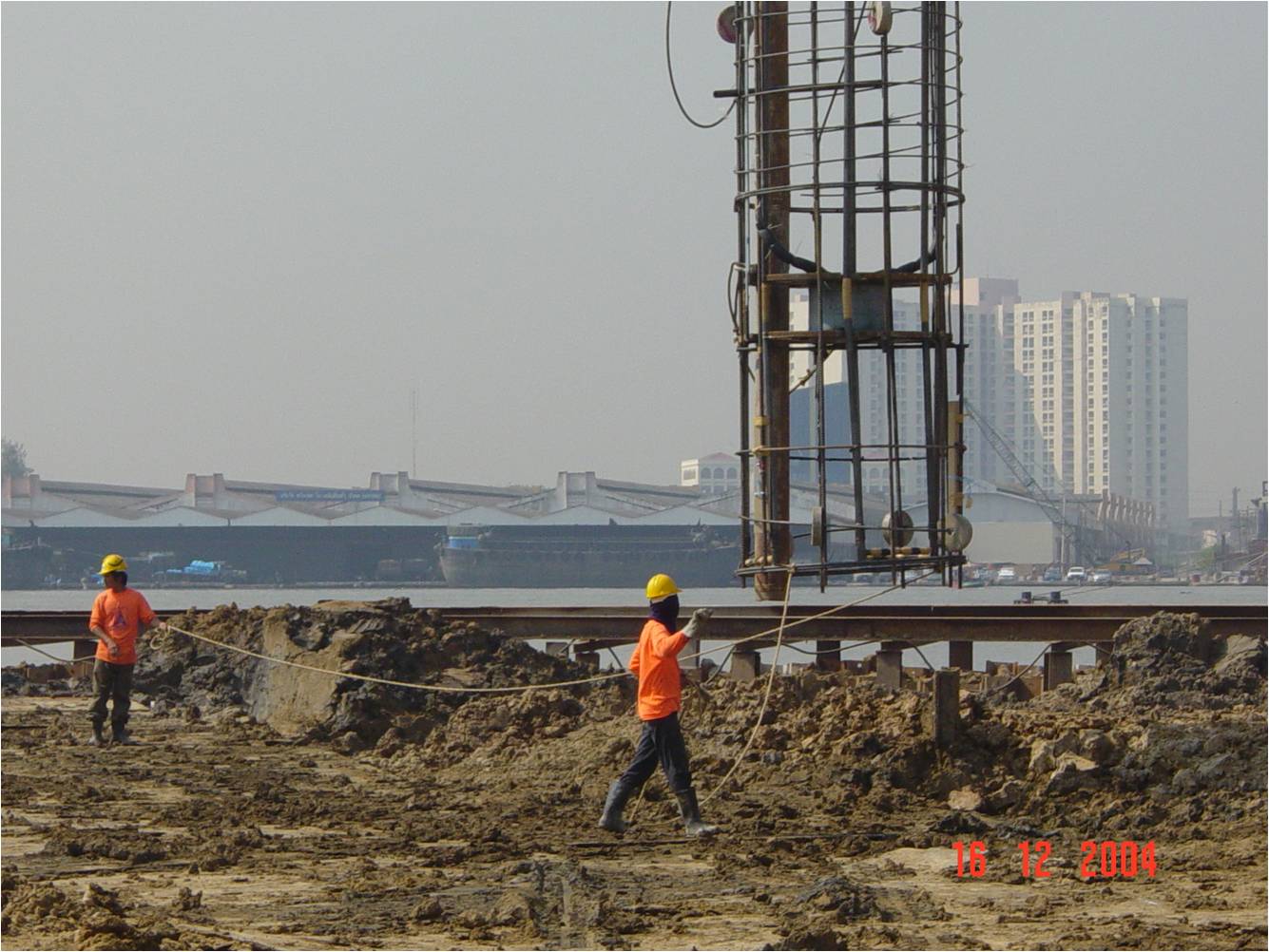
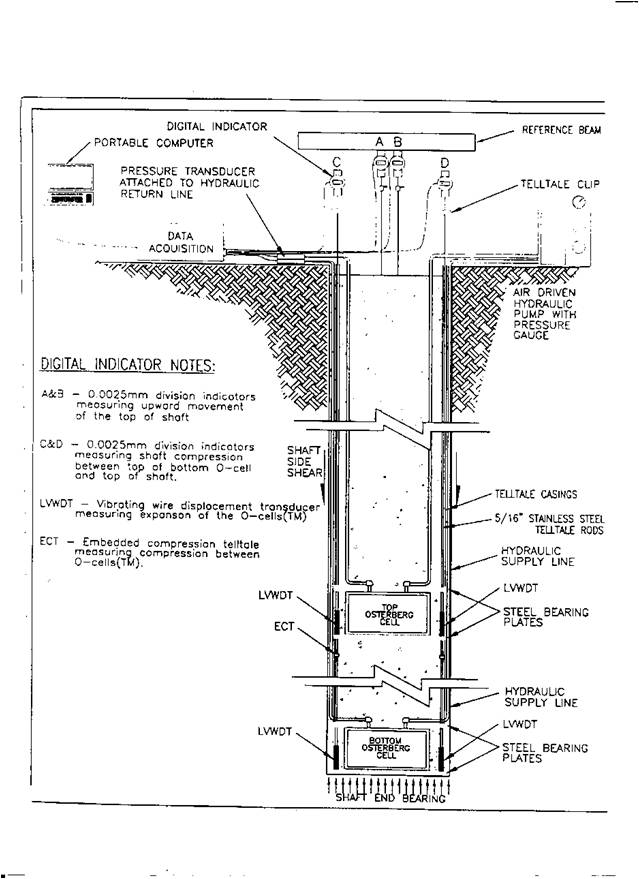
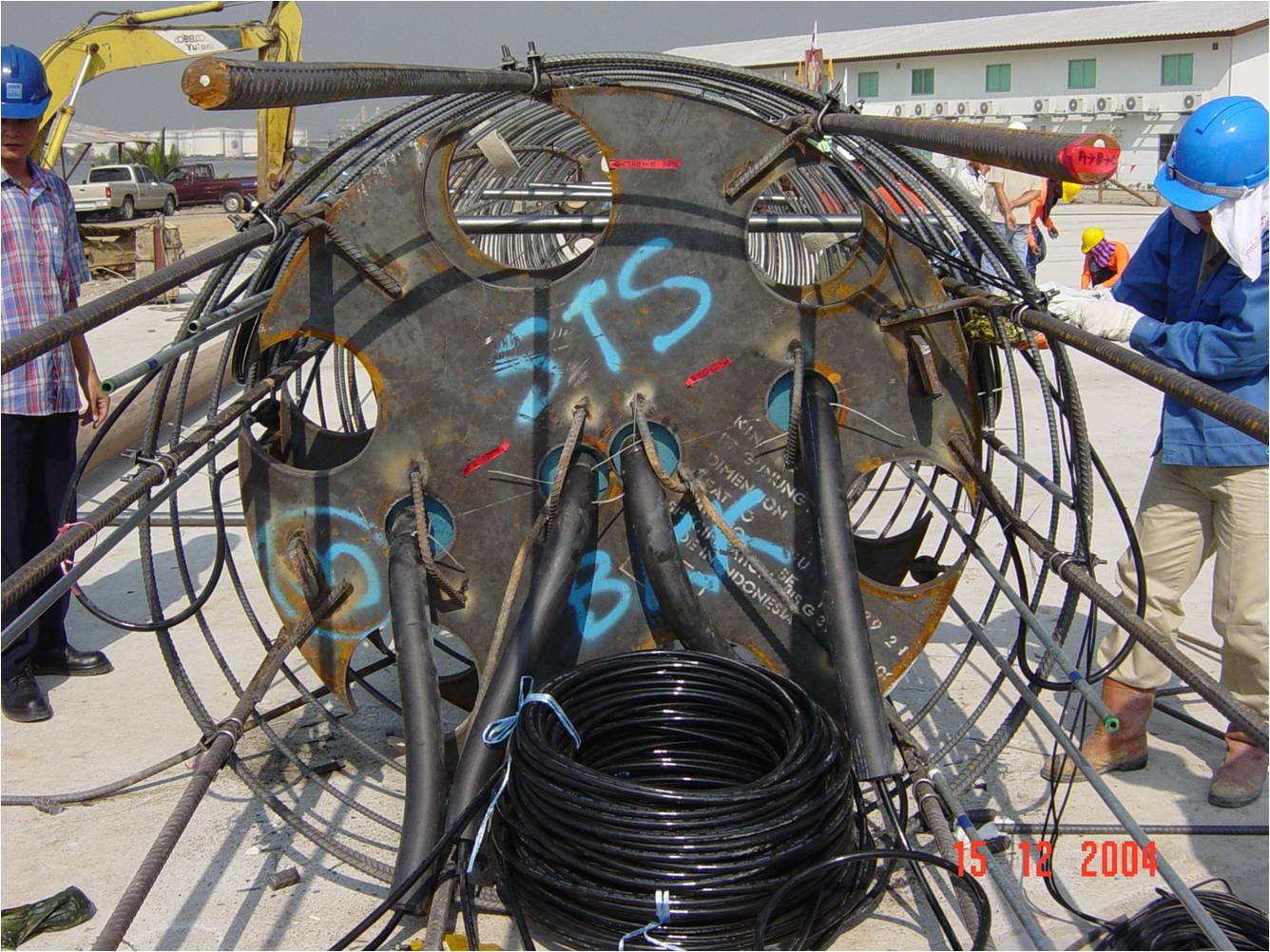
Drilling Hole Monitoring by Koden, model: DM-604, 604R, and 604RR, can measure and confirm for underground foundation work, the state of wall surface, pile diameter, deflection, and incline, namely the "vertical accuracy" of the drilled hole or excavated wall. The deviation of the borehole or trench from the perpendicular and any surface cavities in the borehole or trench wall is measured. The ultrasonic measurement probe is suspended vertically from a cable and lowered into the object to be surveyed. At the same time, orthogonal waves are continuously emitted from the device and reflected from the walls. The reflected waves are registered by measurement sensors. The distances, calculated as a function of wave speed and reflection time, are presented in graphic form.
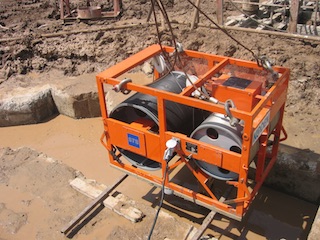
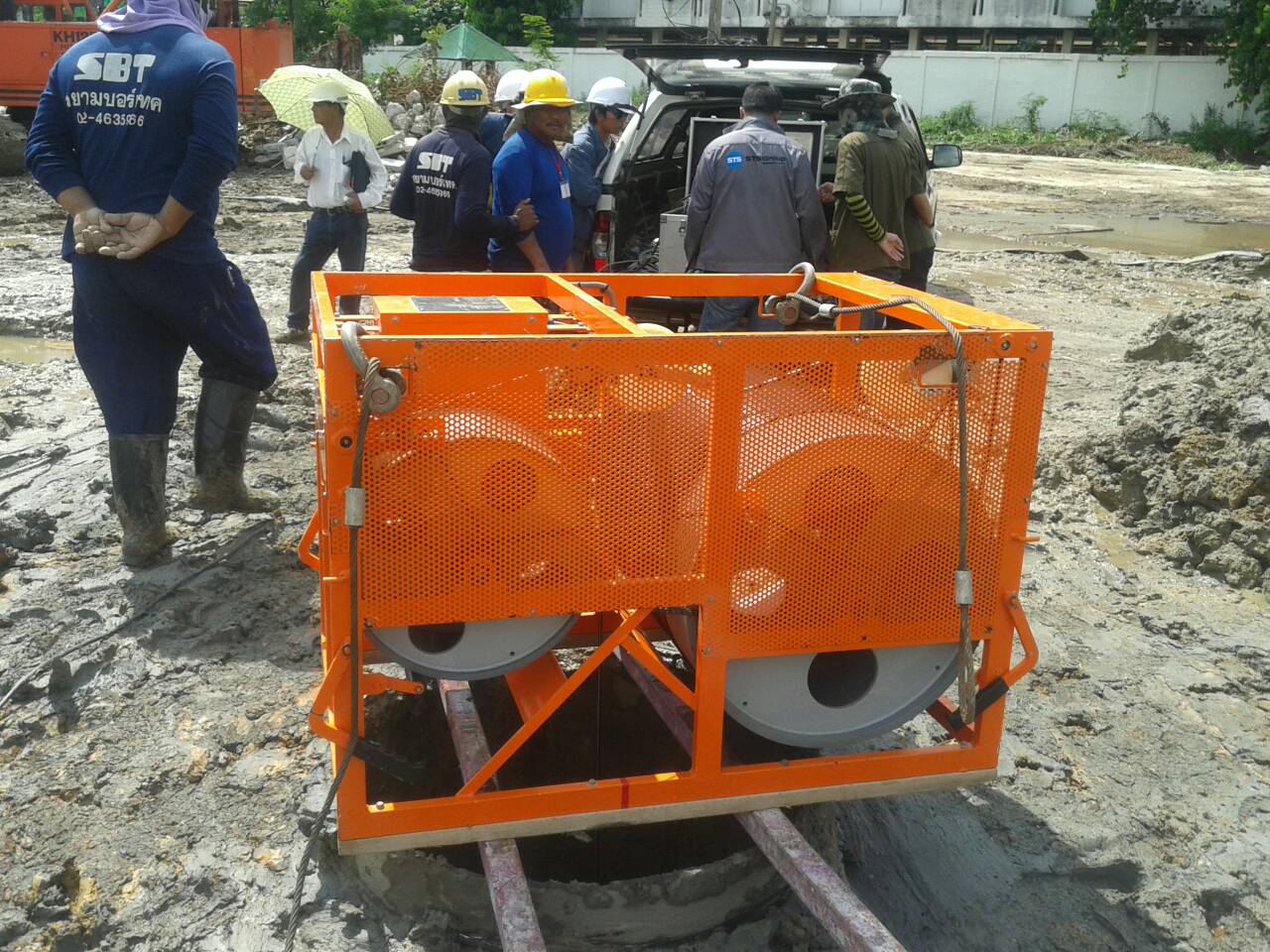
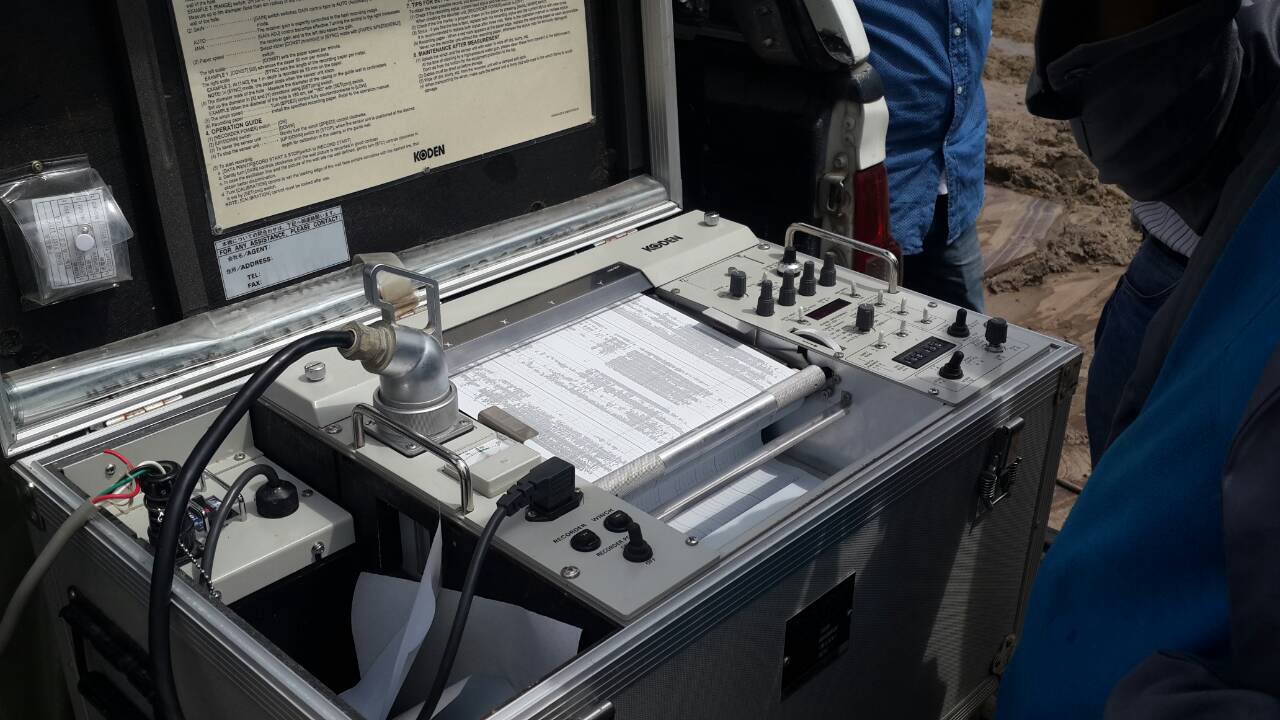
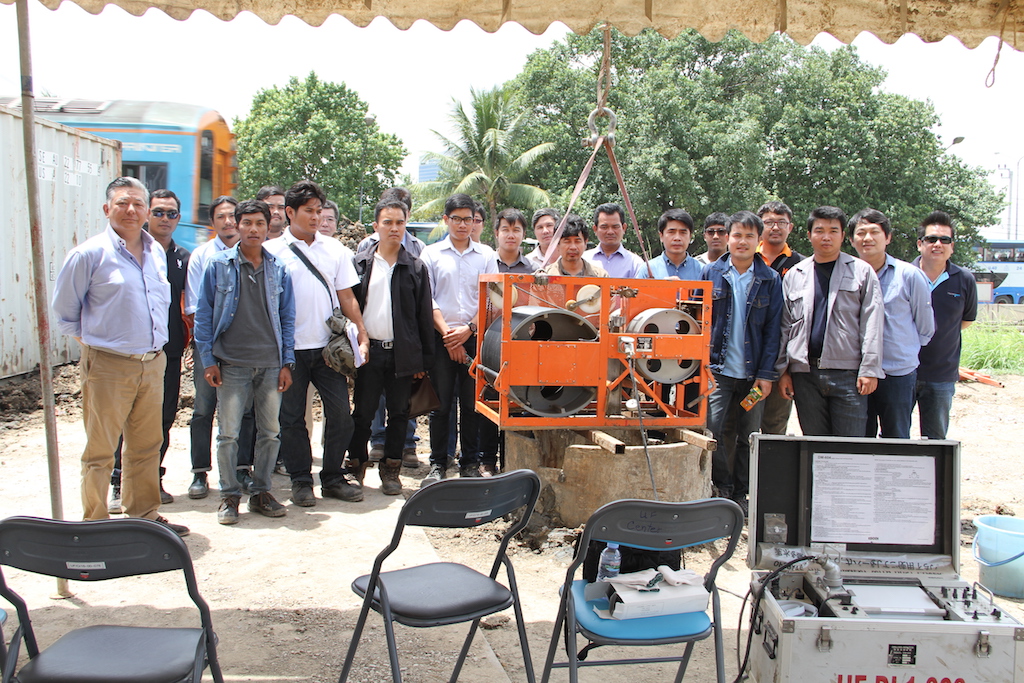
A Parallel Seismic Testing system is designed to determine the length and integrity of foundations when the top is not accessible or when the pile is too long and slender to test with echo techniques or below a buried pile cap. Ultimately, Parallel Seismic testing provides information concerning the length and compression velocity of foundations and can be used on concrete, wood, and steel foundations.
In the Parallel Seismic test method, the exposed top of the foundation is impacted by an impulsive hammer to generate compression waves that travel down the foundation and are refracted to the surrounding soil. The refracted wave arrival is tracked at regular intervals by a hydrophone receiver in a cased borehole. The depth of the foundation is determined by plotting the first arrival times as a function of depth and observing the depth where a change of slope occurs.
For this test method, a borehole must be drilled within 1.00 to 1.50 of the foundation edge and should extend at least 5.00 to 10.00 m. deeper than the anticipated foundation depth. The borehole must be drilled as vertically as possible, cased with steel or PVC pipes, capped at the bottom; and, in the case of hydrophone receivers, be filled with water prior to testing.
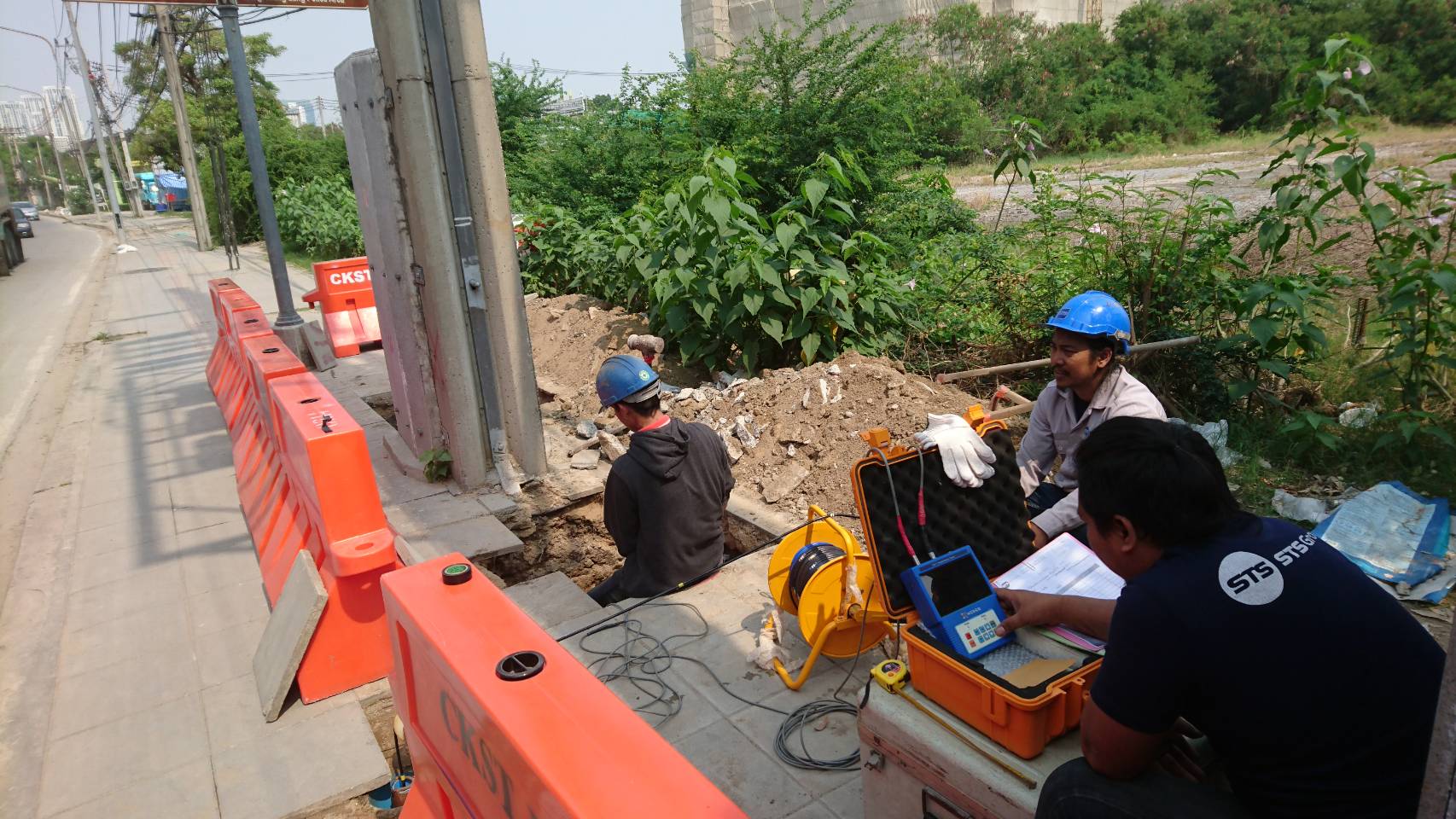
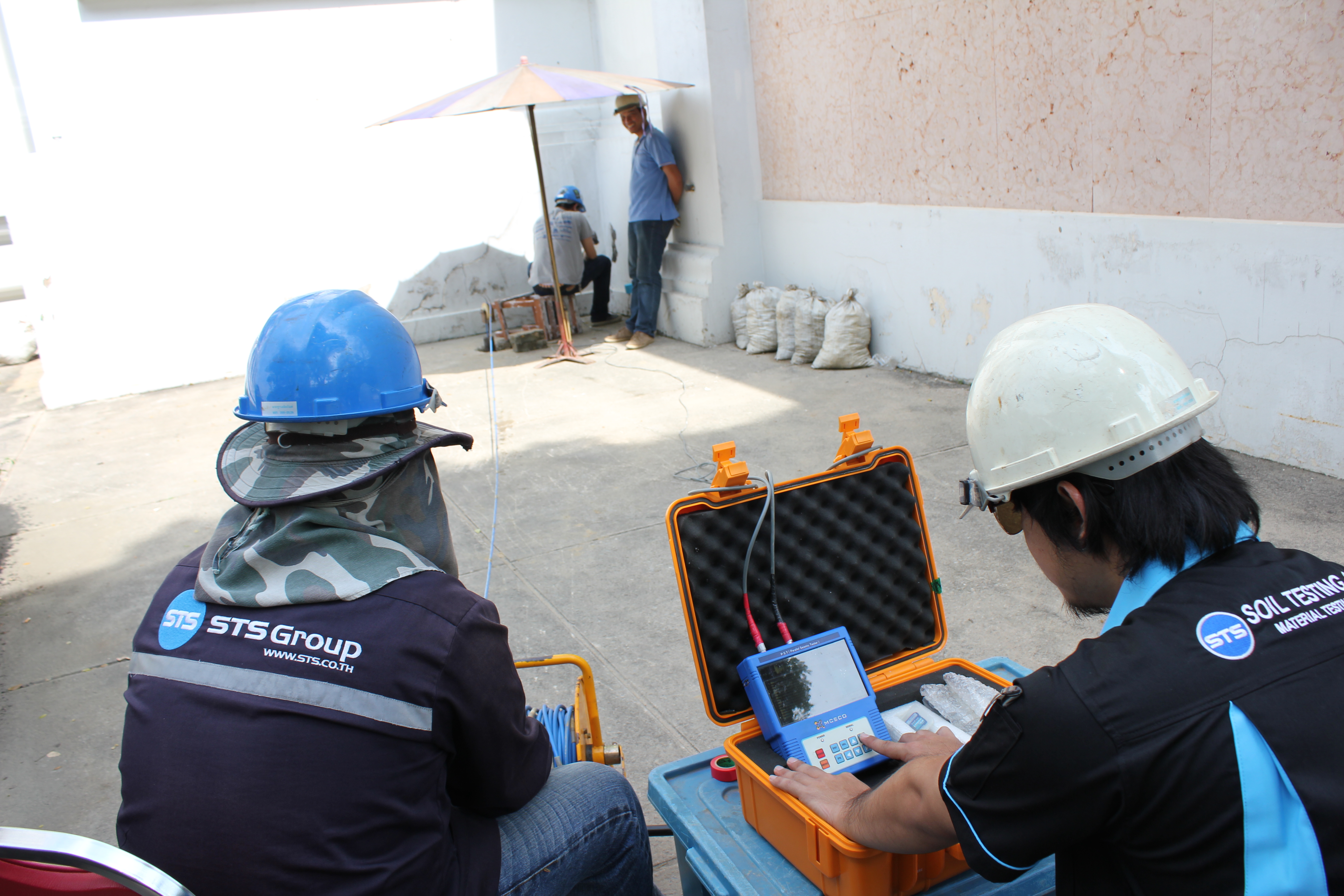